|
Layout-based power-aware signal integrity
Key Benefits
• Performs time domain signal integrity analysis to confirm that designs meet specified targets
• Documents your simulations with flexible 2D and 3D visualization results including waveforms and virtual walk-through
• Provides streamlined workflows for layout-based electrical rule checks (ERCs) using embedded solvers and simulators
Uniquely equipped to let you perform a broad range of analysis tasks from a single tool—including electrical rule checking, interconnect model extraction, signal integrity (SI) and power integrity (PI) studies, and design-stage electromagnetic interference analysis—Cadence® Sigrity™ SPEED2000™ technology is a layout-based finite difference time-domain (FDTD) simulation tool for IC package and/or board analysis with multiple workflows to guide the user through the various analysis tasks. Included is a combination of circuit and transmission-line simulations with a fast, special-purpose electromagnetic field solver that computes dynamic interactions between signal, power, and ground on IC package and board signals and planes.
The Sigrity SPEED2000 technology is designed to work with popular chip/package/board design flows. The tool lets you perform time-domain analysis to confirm that designs meet specified targets, it understands complex voltage noise propagation (including return-path discontinuities), simulates simultaneous switching noise (SSN), and helps you identify improvement opportunities. The Sigrity SPEED2000 technology provides a transient simulation environment for both SI and PI of package and/or PCB. Interconnect model extraction can be performed to support reflection-focused (level 1) or crosstalk-focused (level 2) simulation in a pure circuit simulator such as the Cadence Sigrity SystemSI™ simulator. In addition, the Sigrity SystemSI and SPEED2000 technologies can be used together to support detailed power-aware (level 3) SI analysis using the FDTD-direct workflow.
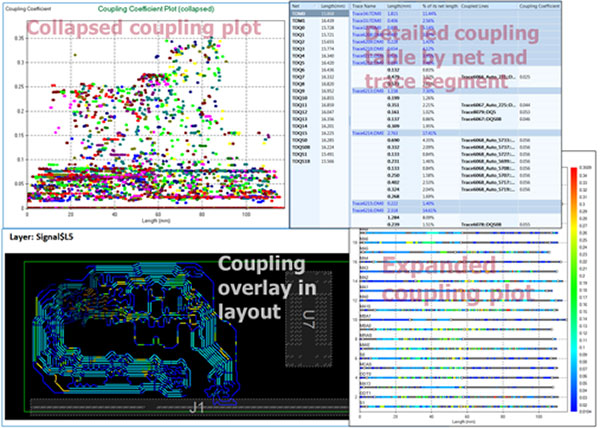 Graphical results from Sigrity SPEED2000 ERC workflows
Another popular Sigrity SPEED2000 workflow is power-aware electrical rule checking (ERC). This unique technology expands beyond classic impedance and crosstalk rule checking by including estimated noise coupling from power and ground planes that may be ringing.
The electro-static discharge (ESD) workflow is used to test the impact of sudden and unexpected flow of electricity from an external source such as human contact or plugging in a cable with a charge. The flow includes defining the placement of an ESD gun model and then observing the impact to the board, signals, and planes. Transient-voltage-suppression (TVS) diodes and their ability to clamp the voltage peak are included in the ESD simulation.
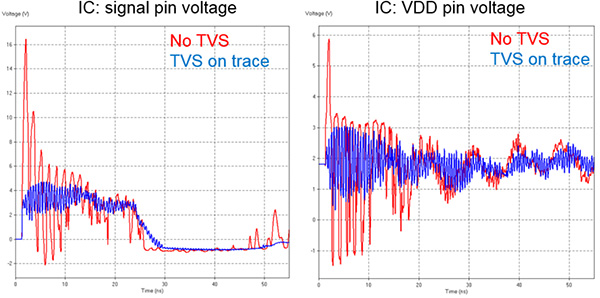 ESD simulation differences with and without transient-voltage-suppression diodes
Features
• Workflows for full board screening of signal impedance, crosstalk, and return path discontinuities (no models required)
• Simulation-based SI rule checking that considers power plane noise (no models required)
• Simulates simultaneous switching noise (SSN) and identifies improvement options
• Unique electromagnetic control (EMC) simulation solution with support for designs with non-linear drivers and receivers
• Determines the impact of variations in stack-up, plane geometries, and I/O configurations
• Observes where noise is generated, identifies how it propagates, and determines if it stays within targeted levels
• Interconnect model extraction of single or coupled signal lines for use with external circuit simulators such as the Sigrity SystemSI tool
• Behaves as an FDTD-direct engine for the Sigrity SystemSI tool, enabling system-level power-aware SI analysis (no requirement for S-parameters)
• ESD workflow provides feedback on effectiveness of TVS diodes
• Optimized for flows with Cadence SiP Layout, Allegro® Package Designer, and Allegro PCB Designer
• Readily used in Mentor, Zuken, and Altium flows, accepting a mix of CAD databases where needed for multi-structure design support
|